Unlocking the potential of technology has revolutionized countless industries, and supply chain management is no exception. With the rise of IoT (Internet of Things) and its seamless integration into our daily lives, businesses are now equipped with powerful tools to optimize their operations like never before. One such application that has gained significant traction is predictive maintenance – a game-changer in ensuring smooth supply chain operations. In this blog post, we will explore the role of IoT in predictive maintenance for supply chain management, delve into its advantages and challenges, highlight real-life examples, and discuss best practices for successful implementation. Strap in as we journey through the world of IoT-powered predictive maintenance!
The Role of IoT in Supply Chain Operations
In today’s fast-paced and highly competitive business environment, supply chain operations play a crucial role in the success of any organization. The ability to effectively manage and optimize the movement of goods from point A to point B is essential for meeting customer demands and maintaining a profitable bottom line.
This is where the Internet of Things (IoT) comes into play. By connecting physical objects, such as vehicles, machinery, and inventory items, to the internet, IoT enables real-time data collection and analysis. This data can then be leveraged to make informed decisions that enhance supply chain efficiency.
One key area where IoT has revolutionized supply chain operations is predictive maintenance. Traditional maintenance practices are often reactive, with repairs being made only after equipment failure occurs. However, with IoT-enabled sensors and monitoring systems in place, organizations can proactively identify potential issues before they escalate into costly breakdowns.
By continuously collecting data on equipment performance and condition, IoT devices can detect anomalies or signs of wear and tear. This allows for timely interventions such as scheduling preventive maintenance or ordering replacement parts before they are urgently needed.
By leveraging artificial intelligence (AI) algorithms to analyze this vast amount of sensor-generated data, organizations can gain valuable insights into patterns and trends that may impact their supply chain operations. These insights help in optimizing processes like inventory management by ensuring optimal stock levels at all times while minimizing excess inventory costs.
Another significant advantage of using IoT for predictive maintenance in supply chain management is improved asset tracking capabilities. With the integration of GPS technology into connected devices within the supply chain network – including delivery trucks or cargo containers – businesses gain real-time visibility over their assets’ location throughout transit.
This level of visibility empowers companies to track shipments accurately from origin to destination while also receiving alerts if there are any delays or deviations from planned routes. Such information allows businesses to proactively address issues that could potentially disrupt their entire supply chain, reducing the risk of costly delays or customer dissatisfaction.
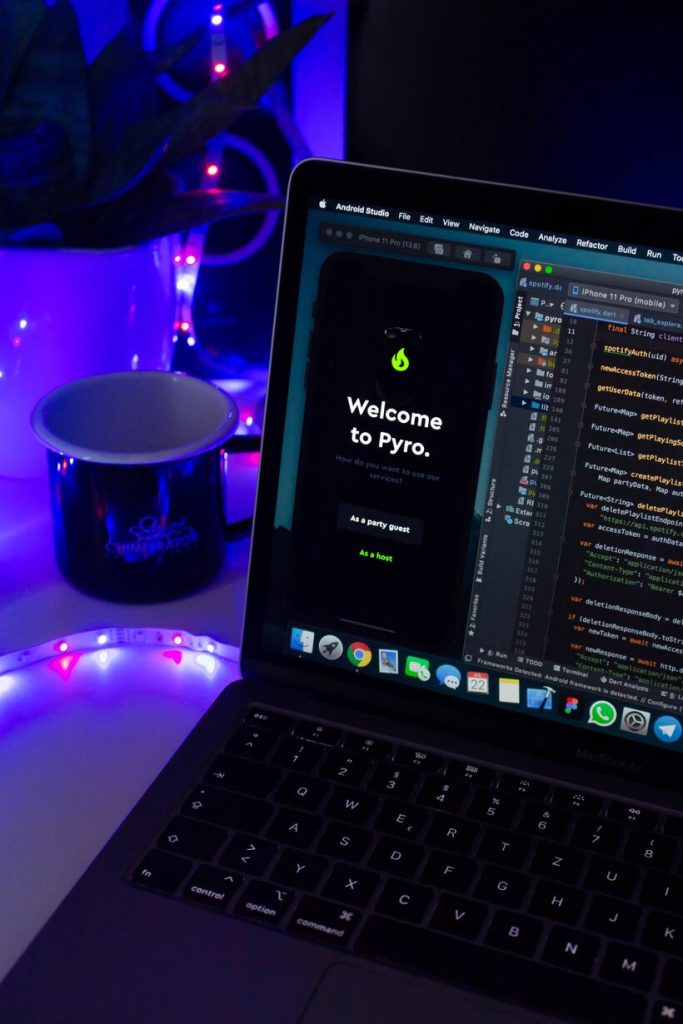
Advantages of Predictive Maintenance in Supply Chain Management
Predictive maintenance, powered by IoT technology, offers numerous advantages for supply chain management. By leveraging real-time data and analytics, organizations can proactively identify and address potential equipment failures or issues before they disrupt operations.
One major advantage is increased machinery uptime. Through continuous monitoring and analysis of equipment performance metrics, predictive maintenance can detect early warning signs of malfunction or wear and tear. This allows for timely repairs or replacements to be scheduled during planned downtime, minimizing unexpected breakdowns that could result in costly production delays.
Another benefit is improved cost-effectiveness. With predictive maintenance, companies can optimize their spare parts inventory by accurately predicting when components will need replacement based on actual usage patterns. This eliminates the need for excessive stockpiling of spares while ensuring that critical items are readily available when required.
Predictive maintenance enhances operational efficiency by reducing unplanned downtime and improving overall equipment effectiveness (OEE). By preventing unexpected failures and optimizing maintenance schedules based on actual asset condition rather than fixed intervals, businesses can maximize productivity while minimizing unnecessary service disruptions.
Implementing IoT-enabled predictive maintenance enables a shift from reactive to proactive decision-making in supply chain operations. Instead of waiting for an issue to occur before taking action, organizations can use real-time insights to make informed decisions aimed at preventing problems from arising in the first place.
This approach helps extend the lifespan of assets through targeted servicing strategies. By identifying potential risks or inefficiencies early on and addressing them promptly through preventive measures such as calibrations or lubrication adjustments, companies can prolong the longevity of their equipment investments.
Real-life Examples of IoT for Predictive Maintenance in Supply Chain Operations
IoT has revolutionized the way businesses approach maintenance in their supply chain operations. By leveraging real-time data and predictive analytics, companies can proactively identify and address potential issues before they escalate into costly disruptions.
One notable example is how General Electric (GE) transformed its manufacturing processes using IoT for predictive maintenance. GE integrated sensors into their machines, enabling them to collect data about performance and health in real-time. This data allowed GE to accurately predict when a machine would require maintenance or repairs, reducing unplanned downtime significantly.
Another success story comes from Schneider Electric, a global leader in energy management and automation. They implemented an IoT-based predictive maintenance system called EcoStruxure Asset Advisor across their supply chain operations. This solution uses advanced analytics to monitor critical assets remotely and provides actionable insights for proactive maintenance activities.
In the transportation industry, FedEx utilizes IoT sensors on their delivery vehicles to track performance metrics such as tire pressure, engine health, fuel efficiency, and more. With this information at hand, FedEx can schedule preventive maintenance tasks efficiently while minimizing vehicle breakdowns that could disrupt deliveries.
These examples highlight the immense value of implementing IoT for predictive maintenance in supply chain operations. By harnessing the power of technology and data-driven insights, businesses can optimize operational efficiency while reducing costs associated with unexpected equipment failures or delays.
Challenges and Limitations of Implementing IoT for Predictive Maintenance
Implementing IoT for predictive maintenance in supply chain operations can come with its fair share of challenges and limitations. One major challenge is the sheer complexity of integrating various IoT devices, sensors, and data analytics platforms into existing supply chain systems. This requires careful planning and coordination to ensure seamless integration without disrupting ongoing operations.
Another challenge is the need for a robust and reliable network infrastructure to support the continuous flow of data between different components of the supply chain ecosystem. Without a stable network connection, real-time monitoring and analysis may be compromised, leading to delays in identifying potential issues or failures.
Security concerns also pose a significant limitation when it comes to implementing IoT for predictive maintenance. With an increasing number of connected devices, there is a higher risk of cyber threats and unauthorized access to sensitive data. Ensuring strong encryption protocols, authentication measures, and regular security updates are crucial to mitigate these risks effectively.
Cost considerations can present another hurdle in adopting IoT for predictive maintenance. While the long-term benefits may outweigh initial investments, businesses must carefully evaluate their budget constraints before committing resources to implement new technologies across their supply chain operations.
Change management within organizations can prove challenging as employees may resist learning new systems or adapting to new processes associated with IoT implementation. Proper training programs should be implemented alongside clear communication strategies to address any resistance or confusion among staff members.
Best Practices for Successful Implementation of IoT for Predictive Maintenance in Supply Chain Operations
1. Define clear objectives: Before implementing IoT for predictive maintenance in your supply chain operations, it is crucial to establish clear goals and objectives. Identify the specific areas where predictive maintenance can improve efficiency and reduce costs.
2. Choose the right technology: Selecting the appropriate IoT devices and sensors is essential for successful implementation. Consider factors such as data accuracy, connectivity options, and compatibility with existing systems.
3. Ensure data quality: Reliable data is fundamental to effective predictive maintenance. Implement robust data collection processes that capture accurate information about equipment performance, usage patterns, and environmental conditions.
4. Establish real-time monitoring capabilities: Real-time monitoring allows you to detect anomalies or potential failures immediately. Set up alerts or notifications that trigger preventive actions before a breakdown occurs.
5. Implement advanced analytics: Make use of sophisticated analytics tools to analyze large volumes of sensor data collected from various sources within your supply chain network. This will enable you to identify patterns, predict failures, and optimize maintenance schedules.
6. Integrate with other systems: To maximize the benefits of IoT for predictive maintenance, integrate the collected data with other relevant systems such as inventory management or production planning software. This integration enables a holistic view of your supply chain operations’ health.
7. Train employees on new workflows: Provide adequate training to employees involved in handling IoT devices, interpreting analytics reports, and executing preventive maintenance tasks based on insights generated by the system.
8. Maintain a proactive approach: Regularly review performance metrics and adjust maintenance strategies accordingly based on real-time insights gained from IoT-enabled devices.
By following these best practices when implementing IoT for predictive maintenance in your supply chain operations, you can enhance operational efficiency while minimizing downtime caused by unforeseen equipment failures.
Future Outlook and Conclusion
As we move forward into the future, it is clear that IoT for predictive maintenance will continue to play a vital role in supply chain operations. The advancements in technology and connectivity have paved the way for more efficient and effective maintenance strategies.
With IoT sensors providing real-time data on equipment performance, supply chain managers can proactively identify potential issues before they escalate into costly breakdowns or disruptions. This not only improves operational efficiency but also reduces downtime and enhances customer satisfaction.
The integration of predictive maintenance with IoT allows businesses to shift from reactive to proactive approaches, ultimately resulting in significant cost savings. By leveraging data analytics and machine learning algorithms, companies can optimize their maintenance schedules, streamline processes, and improve overall productivity.
There may be limitations related to initial costs associated with installing IoT devices or training employees on new technologies. It is crucial for organizations to weigh these factors against the long-term benefits before embarking on an implementation journey.
Embracing IoT technology for predictive maintenance offers numerous advantages within supply chain operations. With improved efficiency in identifying potential failures beforehand coupled with reduced downtime costs through proactive measures; smart devices like sensors offer real-time insights while increasing customer satisfaction levels by reducing disruption timescales significantly!
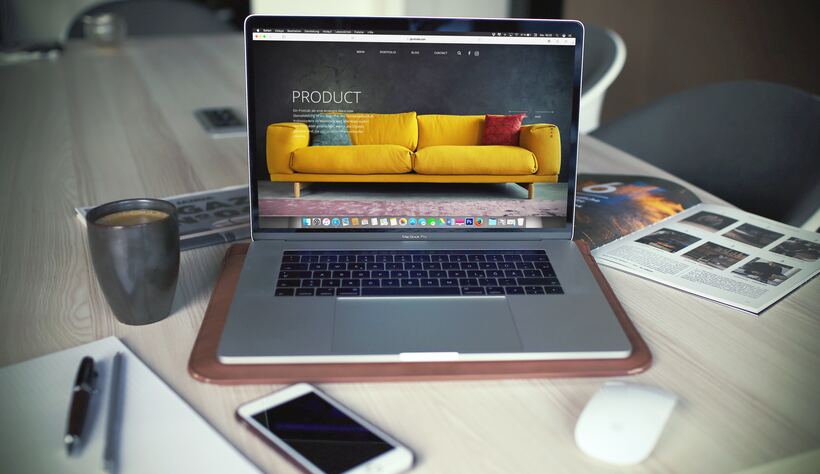
No Comments
Leave a comment Cancel